Welding can be a dangerous business. Every year hundreds of Americans die or are terribly injured in welding accidents. Welding should only be conducted when very strict safety precautions have been taken. This is why you must know everything there is about using welding equipment.
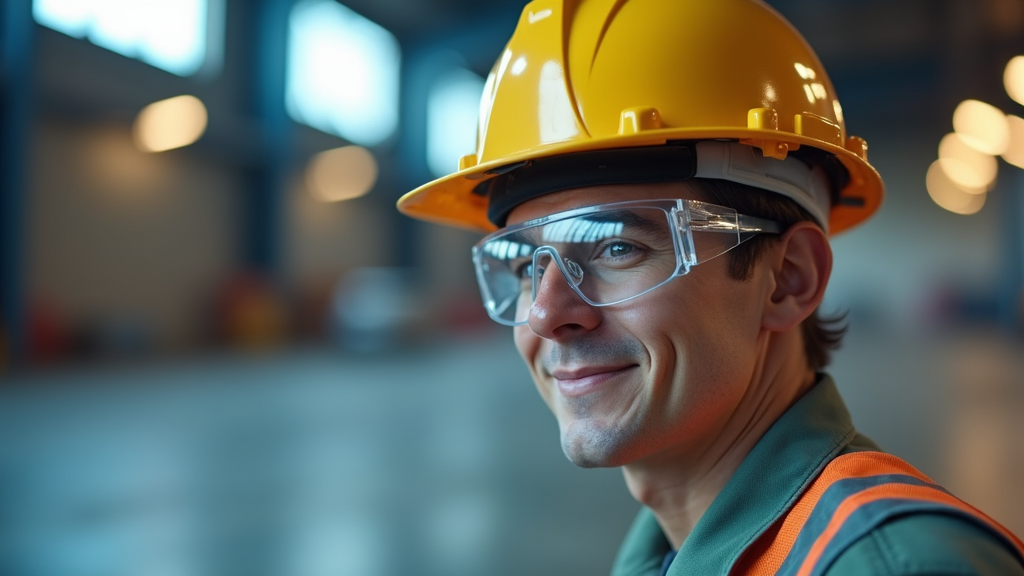
Proper safety gear is essential to avoid mishaps. The high temperatures and intense light associated with welding require the use of specialized protective equipment. Specialized graphite products like shielded helmets and heat shields can also help shield workers from extreme heat. Ensuring you have the right safety gear and following proper protocols can mean the difference between a successful welding project and a devastating accident. This guide will take you through what you need to know.
Safety Welding Equipment You Need
Safety equipment that aids in the correct application of these precautions includes:
Heat Resistant Gloves
Burns are the number one cause of welding injuries in the United States. All welding involves heating surfaces to temperatures of around 3,000 degrees Celsius and above. Special heat-resistant gloves are essential for all welders. Any welder not wearing gloves is putting themselves in terrible danger.
Helmet
A good helmet or mask is necessary when welding. Your face is necessarily very close to some rather dangerous forces when you are fusing surfaces. Heat and electrical arcs can cause serious injury to the face – which a good mask can stop. ‘Arc eye’ is also a huge problem facing welders. Arc eye is an inflammation of the cornea caused by looking directly into the incredibly bright light produced during arc welding. A good welding helmet shields the eye from ultraviolet light produced during the welding process.
Manual SMAW Welder
Shielded metal arc welding is by far the most versatile and commonplace kind of welding used in small workshops and home applications. The type of machine used for Shielded Metal Arc Welding incorporates the use of flux-covered electrode rods. The machine passes a huge current through the electrode rod.
This strikes an arc between the electrode and the bonding surfaces, causing a protective slag to form around the joint as it fuses. This kind of welding machine does not use a protective layer of gas, which makes it far cheaper and easier to use. Despite it being the simplest kind of common welding machine, you should still always seek training before using one of these devices.
Automatic Welding Machines
Although manual welding is perfectly good for most applications, some jobs require more speed and accuracy in order to be completed to a high standard. This is where automatic welding machines come in handy. Automatic welding machines remove some of the most unwelcome variables in manufacturing. This makes them very popular with companies looking to create very uniform products. The machines themselves can be very expensive and often require very accurate programming. If an operation is large enough, however, the costs are soon recouped because fabrication staff is able to work far more efficiently.
Rods
Not all kinds of welding make use of conductor or slag rods. Impact welding, for instance, doesn’t use any kind of conductor at all. Most modern welding processes use rods to both conduct heat and provide a protective slag over the weld joint. Different welding processes use welding rods for different purposes. Accordingly, you might find a welding rod being referred to as either a ‘filler’ or an ‘electrode’. Depending on what kind of materials are in need of welding, different chemical coatings need to be powdered on top of a welding rod metal or plastic core.
Read also:
Leave a Reply